鋁型材機架非標件加工的自制與外協(xié)選擇需基于成本、效率及企業(yè)戰(zhàn)略綜合考量。以下從成本效益角度對比分析兩種策略:
一、自制成本分析
1. 顯性成本:需投入設備折舊、模具開發(fā)、人工、原材料及能源消耗。小批量生產(chǎn)時,設備利用率低導致單件成本偏高,例如CNC設備折舊費用分攤至少量訂單時可能超外協(xié)報價。
2. 隱性成本:技術工人培訓、生產(chǎn)管理及質(zhì)量管控投入增加,若企業(yè)業(yè)務非機加工,易分散資源影響整體效率。
3. 優(yōu)勢場景:適用于大批量標準化零件加工(年需求超500件)或需嚴格保密的部件,長期可降低邊際成本。
二、外協(xié)成本分析
1. 直接成本:按件支付加工費,含材料、工藝及物流費用。加工廠因規(guī)模效應和技術專精,復雜結構件成本通常低于企業(yè)自建產(chǎn)線。
2. 風險成本:需增加供應商管理、質(zhì)量抽檢及溝通成本,交貨延期可能導致項目停滯損失。
3. 優(yōu)勢場景:小批量(50件以內(nèi))、高復雜度或短期項目更具經(jīng)濟性,尤其適合設備投入不足或產(chǎn)能飽和的企業(yè)。
三、決策建議
1. 定量測算:以100件訂單為例,自制總成本若高于外協(xié)報價30%以上,優(yōu)先選擇外協(xié)。
2. 戰(zhàn)略匹配:加工能力非競爭力的企業(yè),外協(xié)可釋放資源聚焦研發(fā)與裝配;需快速響應市場的企業(yè),可保留基礎加工能力,將特殊工藝外包。
3. 動態(tài)平衡:建立"件自制+非標件外協(xié)"的混合模式,通過培養(yǎng)2-3家認證供應商形成彈性供應鏈。
終建議企業(yè)結合訂單規(guī)模、技術門檻及資源稟賦,通過全生命周期成本模型動態(tài)優(yōu)化決策,避免陷入單一策略的路徑依賴。
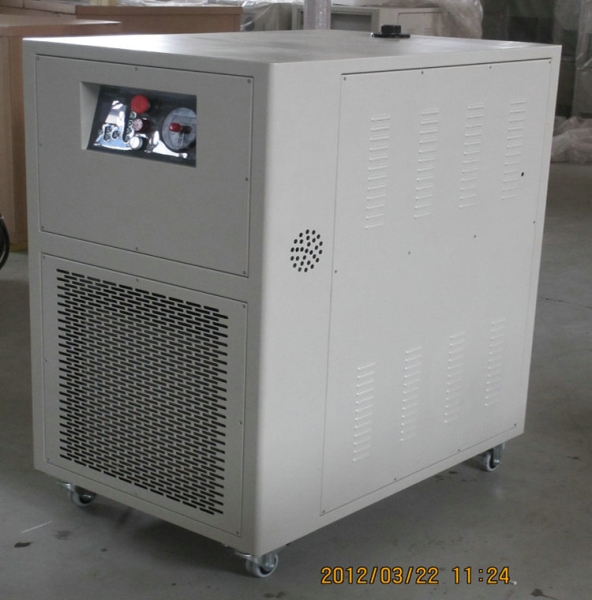